सीएनसी मेसिनिंग त्रुटिहरू
फिक्स्चर फिक्स्चरको ज्यामितीय त्रुटि भनेको वर्कपीसलाई उपकरण र मेसिन उपकरणको सही स्थितिको साथ बराबर बनाउनु हो, त्यसैले फिक्स्चर मेसिनिंग त्रुटिको ज्यामितीय त्रुटि (विशेष गरी स्थिति त्रुटि) ले ठूलो प्रभाव पार्छ।
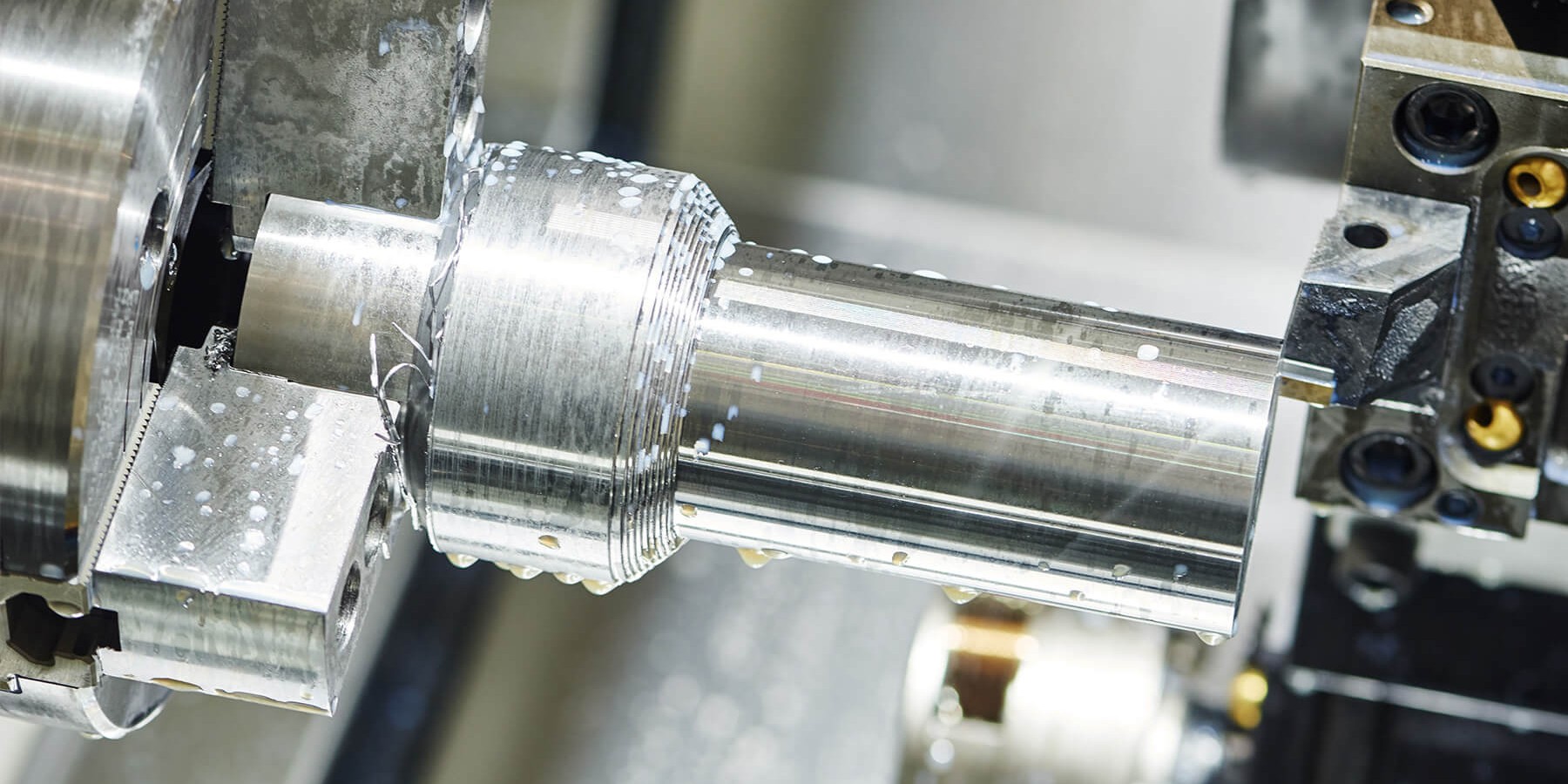
पोजिसनिङ त्रुटिमा मुख्यतया तथ्याङ्कको गलत संयोग त्रुटि र स्थिति निर्धारण जोडीको गलत निर्माण त्रुटि समावेश हुन्छ। जब वर्कपीस मेशिन उपकरणमा प्रशोधन गरिन्छ, प्रशोधनका लागि पोजिसनिङ ड्याटमको रूपमा workpiece मा धेरै ज्यामितीय तत्वहरू चयन गर्न आवश्यक छ। यदि चयन गरिएको पोजिसनिङ ड्याटम र डिजाइन ड्याटम (भाग रेखाचित्रमा सतहको आकार र स्थिति निर्धारण गर्न प्रयोग गरिएको ड्याटम) मिल्दैन भने, यसले ड्याटम बेमेल त्रुटि उत्पन्न गर्नेछ। वर्कपीसको पत्ता लगाउने सतह र फिक्स्चरको पत्ता लगाउने तत्वले सँगै पत्ता लगाउने जोडी गठन गर्दछ। पत्ता लगाउने जोडीको गलत निर्माण र पत्ता लगाउने जोडी बीचको मिलन अन्तरको कारणले गर्दा वर्कपीसको अधिकतम स्थिति भिन्नतालाई लोकेटिंग जोडीको गलत निर्माण त्रुटि भनिन्छ। स्थिति जोडा को निर्माण अशुद्धता त्रुटि समायोजन विधि प्रयोग गर्दा मात्र उत्पादन गर्न सकिन्छ, तर परीक्षण काट्ने विधि मा होइन।
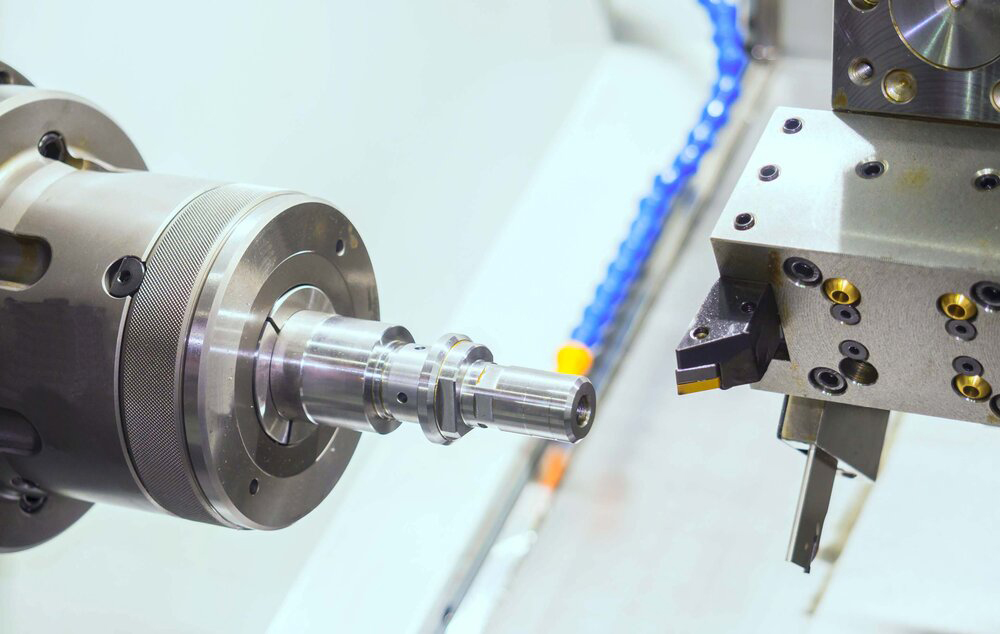
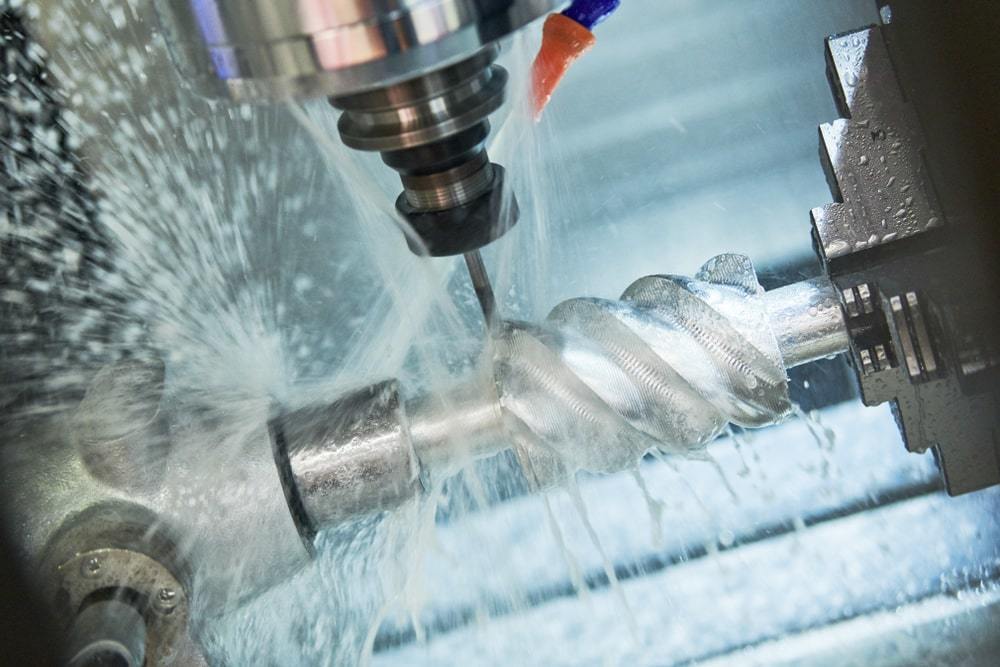
प्रक्रिया प्रणाली विरूपण त्रुटि workpiece कठोरता: प्रक्रिया प्रणाली यदि मेसिन उपकरण, उपकरण, स्थिरता सापेक्ष workpiece कठोरता अपेक्षाकृत कम छ, काट्ने बल को कार्य अन्तर्गत, workpiece को विरूपण को कारण कठोरता को कमी को कारण।मेसिन त्रुटिअपेक्षाकृत ठूलो छ। उपकरणको कठोरता: मेसिनिंग सतहको सामान्य (y) दिशामा बाहिरी गोलाकार घुमाउने उपकरणको कठोरता धेरै ठूलो छ, र यसको विकृतिलाई बेवास्ता गर्न सकिन्छ। सानो व्यासको साथ भित्री प्वाल बोरिंग, उपकरण पट्टी को कठोरता धेरै कमजोर छ, उपकरण पट्टी को बल विरूपण प्वाल को मेसिनिंग शुद्धता मा ठूलो प्रभाव छ।
मेशिन उपकरण पार्ट्स को कठोरता: मेशिन उपकरण भागहरु धेरै भागहरु मिलेर बनेको छ। अहिले सम्म, मेसिन उपकरण पार्ट्स को कठोरता को लागी कुनै उपयुक्त र सरल गणना विधि छैन। वर्तमानमा, यो मुख्य रूपमा प्रयोगात्मक विधि द्वारा निर्धारण गरिन्छ। मेसिन टुल पार्ट्सको कठोरतालाई प्रभाव पार्ने कारकहरूले संयुक्त सतहको सम्पर्क विरूपण, घर्षण बल, कम कठोरता भागहरू र क्लियरेन्स समावेश गर्दछ।
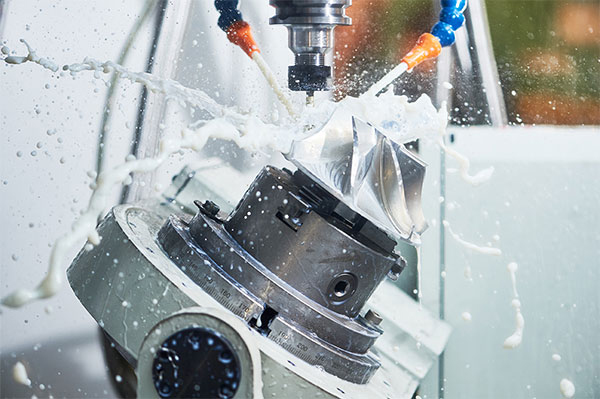
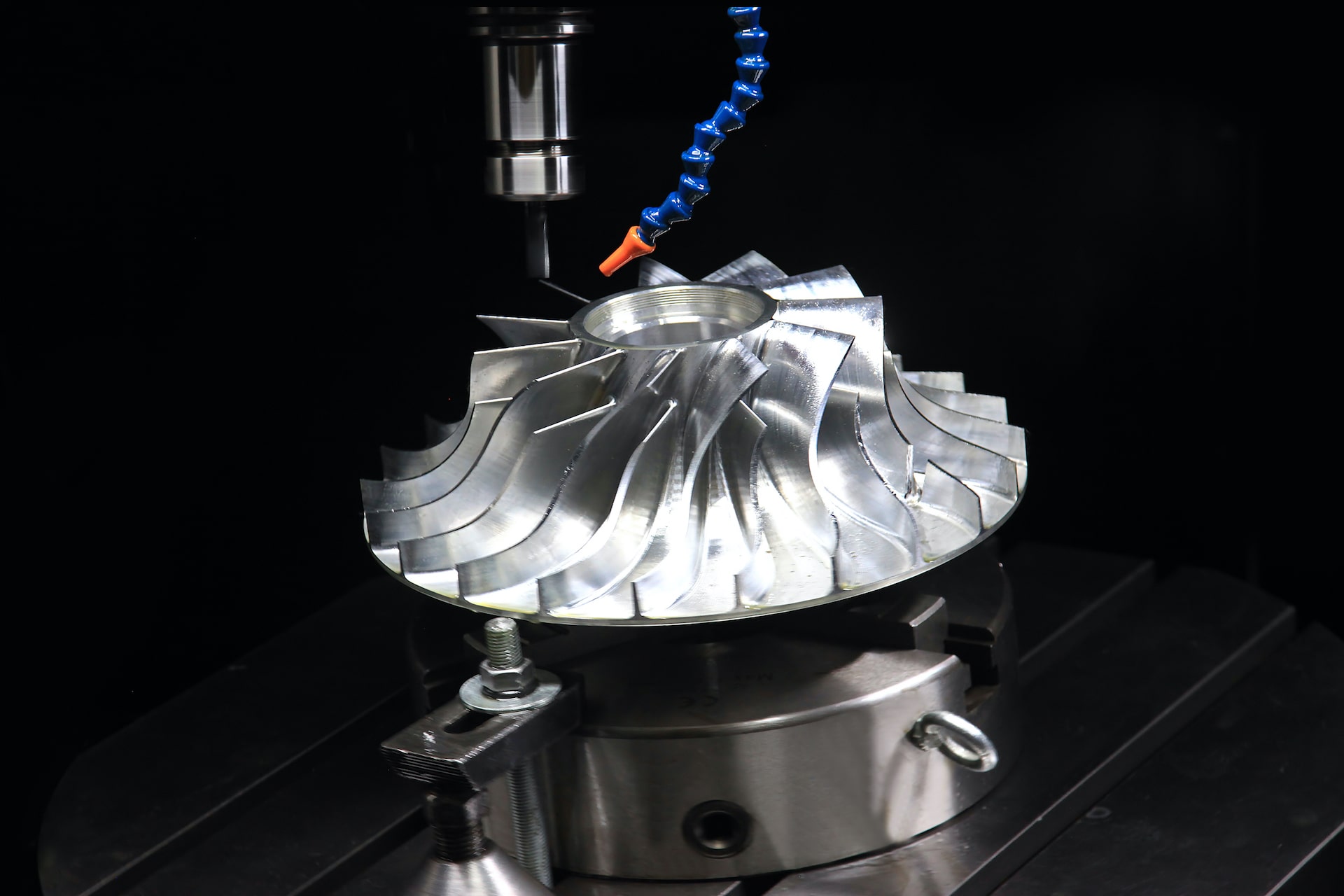
उपकरणको ज्यामितीय त्रुटि काट्ने प्रक्रियामा कुनै पनि उपकरण पहिरन उत्पादन गर्न अपरिहार्य छ, र यसैले workpiece को आकार र आकार परिवर्तन गर्न कारण। मेशिन त्रुटिमा उपकरण ज्यामितीय त्रुटिको प्रभाव विभिन्न प्रकारका उपकरणहरूसँग भिन्न हुन्छ: निश्चित आकार काट्ने उपकरणहरू प्रयोग गर्दा, उपकरणको निर्माण त्रुटिले वर्कपीसको मेसिनिंग शुद्धतालाई सीधा असर गर्छ; यद्यपि, सामान्य उपकरणको लागि (जस्तै टर्निङ उपकरण), निर्माण त्रुटिले मेशिन त्रुटिमा प्रत्यक्ष प्रभाव पार्दैन।